
Plastic Injection Molded Packaging
We help shape the experiences consumers have with our customers' brands, creating the packaging that people want today and solutions to meet their future needs. Shaping by plastic injection is ensuring that we understand our customers'customers. We make packaging that meet consumers'needs ¨C products that shape brand experiences and help fulfill our customer'strategies.
UGI can offer you customized design and finished packaging items to meet your specific needs - a wide range of injection molded plastic packaging and plastic parts, that we have many years of experience processing ABS, Nylon, PC, HIPS, Acrylic, TPE, Acetal, Polypro, PS, and other engineering grade polymers materials.
Plastic boxes
All are manufactured by UGI for domestic use and for export. We produce a large proportion of plastic boxes and plastic packaging that are used in various industries: jewelry boxes, watch boxes, display boxes, presentation boxes, plastic packaging boxes, household storage containers, plastic gift boxes, tool boxes, music boxes, cosmetic boxes etc...
Plastic structured packaging boxes
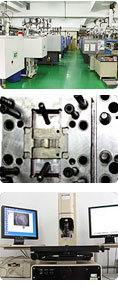
The UGI Packaging offered Product designing and production in a range of Plastics structure packing boxes in different shapes and sizes and for various packaging purposes. The Company's is principal involved in the process of manufacturing all kinds of shaped packaging boxes by injection for packing desktop items, souvenir, household, promotional, gift, wine, pharmaceutical, jewelries, cosmetics, and custom molding for precision packaging needs.
The success and growth of the Company has been made possible by setting the following basic fundamental guidelines -
|
. To maintain customers satisfaction |
Principal Activity
All of our products range are of high quality and are being continuously up-graded to meet market competitiveness and constant changes in consumer / client preferences and requirements.
The Company's development is attributable to the motivation of its staff and management to provide customer satisfaction and confidence of its product quality. The Company's quality control, over 12 years, has lead the name "UGI Packaging" to become a reliable manufacturer of packaging boxes by plastic injection with printing, UV painting, paper & leather mounted finishes.
Our commitment to innovation can be seen in all aspects of our customers' value chain, from brand development to filling and retail display. It is this proposition that positions us as a business partner and not just a supplier.
We shape the experiences enjoyed by our customers, suppliers, employees, and the people living in the societies in which we operate. UGI has been supplying the packaging industry with plastic structured boxes for nearly 12 years. We are a flexible and responsive company that is able to move efficiently towards successful implementation of your new products.
Injection Moulding
UGI is experienced in plastics processing technology, designing, manufacturing and supplying leading edge packaging boxes by our injection and extrusion equipments. Committed to continuous improvements and with a solutions-based approach, we work closely with our customers and supply chains to deliver productivity improvements, technological breakthroughs and market-leading innovations to meet your diversified packaging needs.
Overview
Injection Moulding, along with extrusion ranks as one of the prime processes for producing plastics articles. It is a fast process and is used to produce large numbers of identical items from high precision packaging components to disposable packaging boxes.
Typical Material Used
Most thermoplastics can be processed by Injection Moulding. The below lists some of the commonly used materials especially for packaging purposes:
Acrylonitrile-Butadiene-Styrene ABS
High Impact PS HIPS
Nylon PA
Polycarbonate PC
Polypropylene PP
Polystyrene GPPS
Typical Products Produced
Injection mouldings count for a significant proportion of all plastics products from micro parts to large components such as bumpers and wheelie bins. Virtually all sectors of manufacturing use injection moulded parts - the flexibility in size and and shape possible through use of this process have consistently extended the boundaries of design in plastics and enabled significant replacement of traditional materials thanks to light weighting and design freedom. The table below shows the type of products that can be injection moulded, but is by no means comprehensive.
Power-tool housing | Telephone handsets | Television Cabinets |
Electrical Switches | DVDs | Automotive bumpers |
Automotive dash boards | Battery Casings | Syringes |
Drug Inhalation Units | Disposable razors | Washing-up bowls |
Wheelie bins | Crates/Recycling boxes | Bottle Lids/closures |
Packaging boxes | packaging containers | Packaging accessories |
The Process
The animation linked from this page provides a strong visual description of the injection moulding process.
The essential elements are as follows:
Material is introduced into the injection moulding machine via a Hopper. The injection moulding machine consists of a heated barrel equipped with a reciprocating screw (driven by a hydraulic or electric motor), which feeds the molten polymer into a temperature controlled split mould via a channel system of gates and runners.
The screw melts (plasticises) the polymer, and also acts as a ram during the injection phase. The screw action also provides additional heating by virtue of the shearing action on the polymer.
The polymer is injected into a mould tool that defines the shape of the moulded part.
The pressure of injection is high, dependant on the material being processed; it can be up to one thousand atmospheres. Tools tend to be manufactured from steels, (which can be hardened and plated), and Aluminium alloys for increased cutting and hand polishing speeds. The costs associated with tool manufacture means that injection moulding tends to lend itself to high volume manufacture.
The tool can be used to manufacture one consistent part in a repeating process or incorporate multi cavities (a multi impression tool), that is many components can be manufactured on the same tool repeatedly with a single injection.
Variants of the injection moulding process include multi-shot or 2K moulding (where different materials are injected into the same mould), insert moulding (where metal components are incorporated), structural foam moulding (where the material is foamed to reduce density) and assisted moulding (where gas or water are incorporated to reduce wall thickness).
UGI is a byword for excellence in packaging sectors working for industries as diverse as jewelry, cosmetics, wine, watch, apparel, gift, medical, pharmaceutical, food, domestic appliance, automotive, IT, telecoms and others. Represented worldwide, we are trusted by our customers to offer a wide packaging product range, with machines built to the highest specifications and incorporating the latest technology.
Call us today on + (86) 135 333 11702 or email us [email protected]...and we'll gladly guarantee that you will receive the best product with great satisfaction at a best price!
