Understanding Die Cutting in Packaging: The Role of Molds
Die cutting is a crucial manufacturing process in the packaging industry, where specialized molds (dies) are used to cut and shape materials into desired forms. This process is essential for creating various packaging products, including boxes, labels, and other custom shapes. This article delves into the concept of molds in die cutting, exploring their design, functionality, types, and significance in producing high-quality packaging solutions. Please click here to view our Graphic Design, Printing & Packaging Box showcases, and discuss with our engineers to customize your next printing and gift packaging!
1. What is Die Cutting?
1.1 Definition
Die cutting is a manufacturing process that involves using a die to cut materials into specific shapes and sizes. The die acts as a mold, allowing for consistent and precise cuts in various substrates, including paper, cardboard, plastic, and more.
1.2 Importance in Packaging
In the packaging industry, die cutting is vital for producing customized packaging solutions that meet specific customer needs. It allows for efficient production, reduces waste, and enhances the aesthetic appeal of products.
2. The Role of Molds in Die Cutting
2.1 Definition of Molds
In the context of die cutting, a mold, or die, is a specialized tool designed to create specific shapes by cutting, scoring, or perforating materials. Molds are engineered to withstand the forces applied during the die cutting process and are essential for achieving precision in the final product.
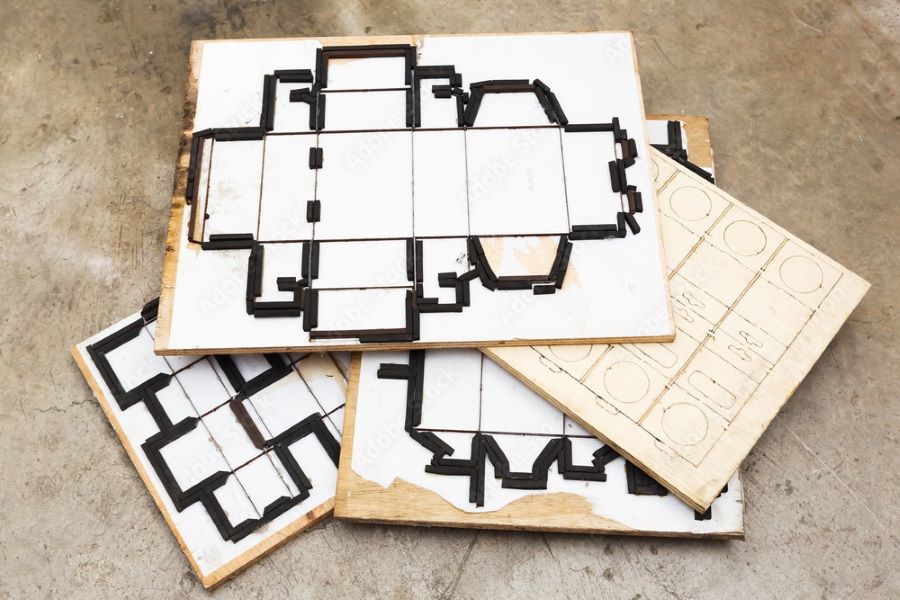
2.2 Types of Molds
2.2.1 Steel Rule Dies
Steel rule dies are made from a thin strip of steel that is bent into the desired shape. They are commonly used for cutting paper and cardboard, offering a cost-effective solution for short to medium production runs.
2.2.2 Flat Dies
Flat dies consist of a flat plate with the cutting edges attached. They are often used in high-speed applications and can accommodate complex designs.
2.2.3 Rotary Dies
Rotary dies use a cylindrical mold that rotates to cut materials as they pass through. This method is efficient for high-volume production and is commonly used in the label and flexible packaging industries.
2.2.4 Custom Dies
Custom dies are designed to meet specific client requirements. These molds can incorporate unique shapes, logos, and other features to enhance branding and product differentiation.
2.3 Materials Used for Molds
The materials used for making molds vary based on the application. Common materials include:
- Steel: Durable and long-lasting, steel is used for high-precision dies.
- Aluminum: Lighter than steel, aluminum is often used for prototypes or lower-volume runs.
- Plastic: Suitable for less demanding applications, plastic molds can be cost-effective for certain projects.
3. The Die Cutting Process
3.1 Preparation
The die cutting process begins with the design phase, where specifications for the mold are established. This includes dimensions, shapes, and any additional features required for the packaging.
3.2 Creating the Mold
Once the design is finalized, the mold is manufactured. This may involve:
- Laser Cutting: For intricate designs, laser cutting technology can create precise molds.
- CNC Machining: Computer Numerical Control (CNC) machining is used for creating molds with high accuracy.
- Handcrafting: Some molds, especially custom ones, may be handcrafted for unique designs.
3.3 Setting Up the Die Cutting Machine
The prepared mold is then installed in a die cutting machine. Proper alignment and calibration are crucial to ensure accurate cutting.
3.4 Cutting Process
During the cutting process, the material is fed into the machine, where the mold applies pressure to cut through the substrate. This may be done using:
- Mechanical Presses: These use mechanical force to drive the cutting process.
- Hydraulic Presses: Hydraulic machines provide consistent pressure, making them suitable for thicker materials.
3.5 Quality Control
After cutting, the produced items undergo quality control checks to ensure they meet specifications. This may include inspecting for cut quality, dimensional accuracy, and overall appearance.
4. Applications of Die Cutting in Packaging
4.1 Retail Packaging
Die cutting is widely used in retail packaging to create eye-catching designs that attract customers. Custom shapes and finishes enhance product visibility on shelves.
4.2 Food Packaging
In the food industry, die cutting is essential for creating packaging that maintains product freshness while providing convenience. This includes boxes, trays, and clamshells.
4.3 E-commerce Packaging
With the rise of e-commerce, die cutting plays a crucial role in producing packaging that protects products during shipping while also providing branding opportunities.
4.4 Cosmetic and Pharmaceutical Packaging
Die cutting allows for the production of elegant packaging that reflects the quality of cosmetic and pharmaceutical products. Custom shapes and finishes enhance the overall appeal.
5. Benefits of Die Cutting with Molds
5.1 Precision and Consistency
Using molds ensures that each cut is precise, resulting in consistent products that meet quality standards.
5.2 Efficiency
Die cutting is a fast process, allowing for high-volume production in shorter time frames compared to manual cutting methods.
5.3 Versatility
Molds can be designed for a wide range of materials, shapes, and sizes, making die cutting a versatile solution for various packaging needs.
5.4 Cost-effectiveness
For large production runs, die cutting can be more cost-effective than other cutting methods, as it reduces material waste and labor costs.
6. Challenges in Die Cutting
6.1 Design Limitations
Complex designs may require specialized molds, which can increase production costs and lead times.
6.2 Material Limitations
Not all materials are suitable for die cutting. Some may require specific types of molds or machinery.
6.3 Wear and Tear
Molds can wear out over time, requiring maintenance or replacement, which can impact production schedules.
Contact us right now!
Die cutting is an essential process in the packaging industry, with molds playing a critical role in shaping materials into functional and visually appealing products. Understanding the various types of molds, their applications, and the die cutting process itself is vital for manufacturers aiming to produce high-quality packaging solutions. As technology continues to evolve, the capabilities of die cutting will expand, offering even more possibilities for customization and innovation in packaging design.
Interested in exploring the application of these custom design & surface treatment processes in printing & packaging products? Click here to access our online showcases & guides…
Here at UGI, we design and manufacture various boxes for many industries:
Advertising boxes; bakery boxes; bottle boxes; candies boxes; cardboard boxes; drawer boxes; cigarettes boxes; file storages boxes; heart shaped boxes; medicine packaging; moving boxes; packaging gift boxes; paperboard packaging; product boxes; protective packaging; retail boxes; shipping cartons; napkin boxes; chipboard boxes; fruit vegetable boxes; electronic packaging boxes; card boxes; craft boxes; lunch boxes; display boxes; folding boxes; clear boxes; mailing boxes; chocolate boxes; cloth boxes; cake boxes; candle boxes; and as well as many others…
WORKING PROCESS
In order to get a smooth process to fulfill your order we suggest you follow below working process with UGI Packaging:
- Request a quote based on the specifications you require via email. Include any photos, images, art design, or technical sketch that could be helpful.
- If you have a similar or identical box to that which you require, send it (via UPS, TNT, DHL, or FEDEX) only after you are satisfied with our quote has been received.
- UGI Packaging will then provide you with a sample and a final quote with our technical sketch in PDF, AI, or CDR format. We will charge you for the sample or prototype development, but it should only be a nominal amounts. After receive your formal order, we will refund the sample charge as our negotiation.
- If you approve the sample then place your order and sign the contract, with 40% advance payment from you, we will start production.
- If any significant changes need to be made to the sample we strongly recommend checking 2nd samples from us before you confirm the final version.
Connect with us on WhatsApp to discuss your next packaging design solution with our manufacturing!