Die Cutting manufacturing process in Paper Packaging
Die cutting is a crucial process in the paper packaging industry, particularly for creating intricate designs and shapes that enhance the aesthetic appeal and functionality of packaging products. This technique is widely employed in producing packaging boxes, labels, and various other paper products. This article delves into the die cutting process, examining its technical aspects, production methods, equipment, and its significance in creating high-quality paper packaging solutions. Please click here to view our Graphic Design, Printing & Packaging Box showcases, and discuss with our engineers to customize your next printing and gift packaging!
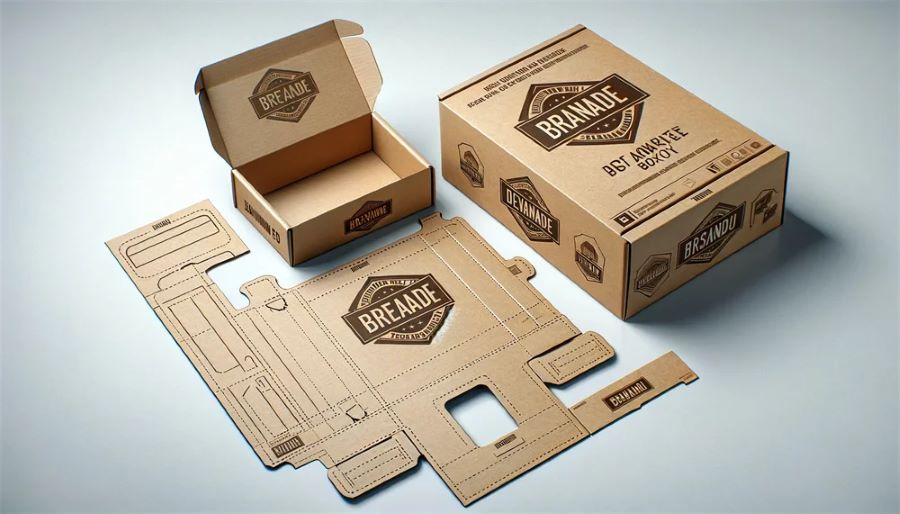
1. Understanding Die Cutting
1.1 Definition
Die cutting is a manufacturing process that involves the use of a die to cut specific shapes or designs out of materials such as paper, cardboard, or plastic. In the context of paper packaging, die cutting allows for the creation of custom shapes that can enhance the presentation and usability of packaging products.
1.2 Types of Die Cutting
- Flat-bed Die Cutting: Utilizes a flat die mounted on a press to cut through the material. This method is suitable for large production runs and intricate designs.
- Rotary Die Cutting: Employs a cylindrical die that rotates against a flat surface, allowing for continuous production. This technique is efficient for high-volume runs.
- Laser Die Cutting: Uses a laser to cut the material, providing high precision and the ability to create complex designs without the need for physical dies.
2. Technical Aspects of Die Cutting
2.1 Materials Used
Different types of paper and board are used in die cutting, including:
- Corrugated Board: Ideal for shipping boxes due to its strength.
- Solid Board: Used for high-end packaging, providing a premium feel.
- Paperboard: Commonly used for lightweight packaging and consumer goods.
2.2 Die Cutting Process
The die cutting process can be broken down into several key steps:
- Design Creation: Utilizing CAD software, designers create the die line that specifies the shape and dimensions of the cut.
- Die Preparation: The die is manufactured based on the design. This can involve cutting steel rules and mounting them on a base.
- Material Setup: The chosen material is loaded into the die cutting machine.
- Cutting: The machine applies pressure to the die, cutting through the material to create the desired shapes.
- Finishing: Post-cutting processes may include stripping away excess material, embossing, or applying surface finishes.
3. Production Considerations
3.1 Batch Sizes
Die cutting is suitable for both large and small batch sizes. However, the efficiency of the process increases with larger runs, making it cost-effective for high-volume production.
3.2 Quality Control
Quality control is vital in the die cutting process to ensure consistency and precision. This involves inspecting the dies, the cutting process, and the final products to meet specified standards.
3.3 Customization
One of the primary advantages of die cutting is the ability to customize designs. This flexibility allows manufacturers to produce unique packaging solutions that meet specific customer needs.
4. Equipment Used in Die Cutting
4.1 Die Cutting Machines
The type of machine used can vary based on the die cutting method:
- Flat-bed Presses: Commonly used for both small and large runs, providing versatility in design.
- Rotary Die Cutters: Ideal for high-speed production, often used in packaging for consumer goods.
- Laser Cutters: Provide precise cuts for intricate designs but may be slower than traditional methods for large runs.
4.2 Maintenance and Calibration
Regular maintenance of die cutting machines is essential to ensure optimal performance. This includes checking the alignment of the die, maintaining cutting blades, and calibrating pressure settings to achieve consistent results.
5. The Die Cutting Process in Action
5.1 Step-by-Step Workflow
- Design Approval: Finalizing the design with the client.
- Die Creation: Manufacturing the die according to the approved design.
- Material Selection: Choosing the appropriate material based on the product requirements.
- Cutting Operation: Running the die cutting machine with specified pressure and speed.
- Post-Cutting Processing: Removing excess material and adding any additional finishes.
5.2 Case Study: High-End Gift Packaging
An example of die cutting’s application can be seen in high-end gift packaging. A manufacturer may create a custom-shaped box with intricate designs on the lid. The die cutting process allows for precision in the cuts, ensuring that the box closes perfectly and maintains its structural integrity.
6. Surface Finishes in Die Cutting
6.1 Importance of Surface Finishes
Surface finishes enhance the visual appeal and tactile quality of packaging. Common finishes include:
- Gloss or Matte Lamination: Provides a protective layer and enhances the appearance.
- Foil Stamping: Adds metallic accents to designs, making them stand out.
- Embossing/Debossing: Creates a three-dimensional effect, adding texture to packaging.
6.2 Integration of Surface Finishes
The die cutting process can be combined with surface finishing techniques in a single workflow, streamlining production and ensuring consistency across the final product.
7. Challenges in Die Cutting
7.1 Material Limitations
Some materials may not be suitable for die cutting due to their thickness or composition, which can limit design options.
7.2 Precision Issues
Achieving high precision can be challenging, especially with intricate designs. Regular calibration and quality checks are essential to maintain standards.
7.3 Cost Considerations
While die cutting is cost-effective for large runs, initial setup costs for dies can be high, making it less economical for small batches.
8. Future Trends in Die Cutting
8.1 Technological Advancements
Advancements in technology, such as automation and improved laser cutting techniques, are expected to enhance the efficiency and versatility of die cutting processes.
8.2 Sustainability Practices
As sustainability becomes increasingly important, manufacturers are exploring eco-friendly materials and processes in die cutting to reduce environmental impact.
8.3 Customization Demand
With growing consumer preferences for personalized products, the demand for custom die-cut packaging solutions is likely to increase.
Contact us right now!
Die cutting plays a vital role in the paper packaging industry, especially for creating high-quality, custom-designed products. By understanding the technical aspects, production methods, and equipment involved, manufacturers can leverage die cutting to produce innovative packaging solutions that meet market demands. As the industry evolves, staying abreast of technological advancements and sustainability practices will be key to maintaining competitiveness.
Interested in exploring the application of these custom design & surface treatment processes in printing & packaging products? Click here to access our online showcases & guides…
Here at UGI, we design and manufacture various boxes for many industries:
Advertising boxes; bakery boxes; bottle boxes; candies boxes; cardboard boxes; drawer boxes; cigarettes boxes; file storages boxes; heart shaped boxes; medicine packaging; moving boxes; packaging gift boxes; paperboard packaging; product boxes; protective packaging; retail boxes; shipping cartons; napkin boxes; chipboard boxes; fruit vegetable boxes; electronic packaging boxes; card boxes; craft boxes; lunch boxes; display boxes; folding boxes; clear boxes; mailing boxes; chocolate boxes; cloth boxes; cake boxes; candle boxes; and as well as many others…
WORKING PROCESS
In order to get a smooth process to fulfill your order we suggest you follow below working process with UGI Packaging:
- Request a quote based on the specifications you require via email. Include any photos, images, art design, or technical sketch that could be helpful.
- If you have a similar or identical box to that which you require, send it (via UPS, TNT, DHL, or FEDEX) only after you are satisfied with our quote has been received.
- UGI Packaging will then provide you with a sample and a final quote with our technical sketch in PDF, AI, or CDR format. We will charge you for the sample or prototype development, but it should only be a nominal amounts. After receive your formal order, we will refund the sample charge as our negotiation.
- If you approve the sample then place your order and sign the contract, with 40% advance payment from you, we will start production.
- If any significant changes need to be made to the sample we strongly recommend checking 2nd samples from us before you confirm the final version.
Connect with us on WhatsApp to discuss your next packaging design solution with our manufacturing!