A Revolutionary Surface Finish for Paper Packaging Boxes
When it comes to creating visually stunning and high-impact packaging, the choice of surface finishes plays a critical role. Among the many surface finishing techniques available, Cast & Cure has emerged as an innovative, eco-friendly, and cost-effective solution. Known for its ability to produce dazzling visual effects, Cast & Cure combines functionality with aesthetic appeal, making it a popular choice for brands looking to elevate their packaging designs. Please click here to view our Graphic Design, Printing & Packaging Box showcases, and discuss with our engineers to customize your next printing and gift packaging!
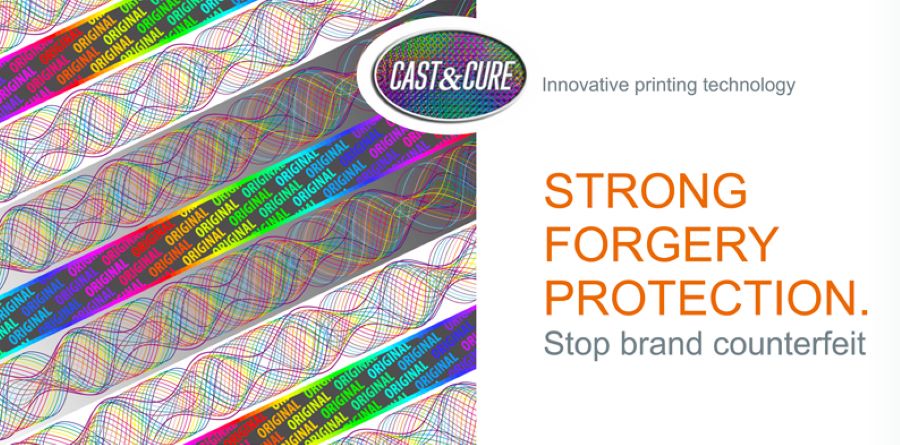
In this comprehensive article, we’ll explore the Cast & Cure process, its benefits, applications in paper packaging, and its role in shaping the future of sustainable packaging solutions.
Table of Contents
- What is Cast & Cure?
- How Does the Cast & Cure Process Work?
- Key Features of Cast & Cure Finishes
- Advantages of Cast & Cure in Paper Packaging
- Cost-Effectiveness
- Sustainability
- Aesthetic Versatility
- Applications of Cast & Cure in Packaging
- Luxury Packaging
- Food and Beverage Packaging
- Cosmetic and Personal Care Packaging
- Types of Effects Achievable with Cast & Cure
- Glossy and Matte Effects
- Holographic Patterns
- Textured Finishes
- Comparison with Other Finishing Techniques
- Cast & Cure vs. Foil Stamping
- Cast & Cure vs. UV Coating
- Sustainability and Environmental Impact
- Cast & Cure in the Packaging Industry: Case Studies
- The Future of Cast & Cure in Paper Packaging
1. What is Cast & Cure?
Cast & Cure is an innovative surface finishing technique that combines traditional UV coating with a casting film to create striking visual effects on packaging surfaces. The process involves applying a UV varnish or coating to a substrate, which is then “cast” using a reusable patterned film to transfer the desired effect. Once cured under UV light, the film is removed, leaving behind a high-quality finish that enhances the product’s appearance and appeal.
The unique feature of Cast & Cure is its ability to produce a wide range of effects, including holographic patterns, matte finishes, and high-gloss designs, all while being more environmentally friendly than other finishing methods like foil stamping or lamination.
2. How Does the Cast & Cure Process Work?
The Cast & Cure process involves several steps, each contributing to the precision and quality of the final finish:
- Application of UV Coating:
A thin layer of UV varnish or coating is applied to the surface of the paper substrate. This coating forms the base layer that will hold the desired finish. - Casting Film Placement:
A specially designed casting film—featuring the desired pattern or texture—is placed over the wet UV coating. The film acts as a mold, transferring its design onto the coating. - UV Curing:
The substrate, with the casting film in place, passes through a UV curing system. The UV light cures the coating, hardening it and locking the pattern or texture in place. - Removal of Casting Film:
Once the coating is cured, the casting film is peeled away and can be reused for subsequent applications. The result is a flawless, high-quality finish that mimics the pattern or texture of the casting film.
This process is highly efficient and can be easily integrated into existing printing and finishing workflows, making it a versatile solution for packaging applications.
3. Key Features of Cast & Cure Finishes
Cast & Cure offers several distinctive features that set it apart from other surface finishing techniques:
- Reusable Casting Film: The casting film can be reused multiple times, reducing material waste and lowering production costs.
- Customizable Effects: From holographic patterns to matte finishes, Cast & Cure allows for a wide range of design possibilities.
- Eco-Friendly Process: The process uses minimal materials and avoids the need for additional adhesives or foils, making it more sustainable.
- Durable and High-Quality: The cured finish is resistant to scratches, smudges, and fading, ensuring long-lasting visual appeal.
4. Advantages of Cast & Cure in Paper Packaging
4.1 Cost-Effectiveness
Compared to traditional finishing methods like foil stamping or lamination, Cast & Cure is more cost-effective. The reusable casting film significantly reduces material costs, while the process itself is faster and requires fewer resources.
4.2 Sustainability
Cast & Cure is an environmentally friendly alternative to foil stamping and laminates. The reusable nature of the casting film minimizes waste, and the process eliminates the need for non-biodegradable materials.
4.3 Aesthetic Versatility
With Cast & Cure, brands can achieve a wide variety of finishes, including holographic, glossy, matte, and textured effects. This versatility makes it suitable for a broad range of industries, from luxury goods to everyday products.
5. Applications of Cast & Cure in Packaging
5.1 Luxury Packaging
High-end brands in industries like fashion, jewelry, and electronics use Cast & Cure finishes to create premium packaging that stands out on shelves and communicates a sense of exclusivity.
5.2 Food and Beverage Packaging
Cast & Cure is increasingly popular in food and beverage packaging, where holographic or glossy finishes can enhance the appeal of products like chocolates, wine, and gourmet snacks.
5.3 Cosmetic and Personal Care Packaging
The beauty industry relies on Cast & Cure to achieve eye-catching designs that reflect the elegance and sophistication of their products.
6. Types of Effects Achievable with Cast & Cure
6.1 Glossy and Matte Effects
Cast & Cure can create high-gloss or soft matte finishes that add depth and dimension to packaging designs.
6.2 Holographic Patterns
Holographic effects are among the most popular applications of Cast & Cure, offering a dynamic, light-reflecting surface that captures attention.
6.3 Textured Finishes
With the right casting film, brands can achieve unique textures that enhance the tactile appeal of their packaging.
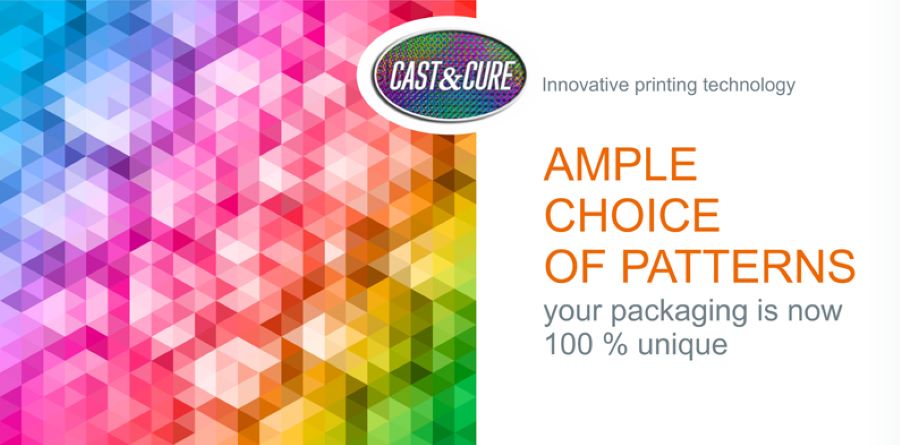
7. Comparison with Other Finishing Techniques
7.1 Cast & Cure vs. Foil Stamping
While foil stamping offers metallic effects, it is less sustainable and more expensive than Cast & Cure. Additionally, Cast & Cure offers greater design versatility.
7.2 Cast & Cure vs. UV Coating
UV coating alone lacks the ability to create textured or patterned effects, making Cast & Cure a more versatile option.
8. Sustainability and Environmental Impact
One of the most significant advantages of Cast & Cure is its eco-friendliness. The process eliminates the need for single-use materials like foils or laminates, and the reusable casting film reduces waste. Additionally, the UV-curing process consumes less energy compared to other finishing techniques, further enhancing its sustainability credentials.
9. Cast & Cure in the Packaging Industry: Case Studies
Case Study 1: Luxury Chocolate Packaging
A premium chocolate brand used holographic Cast & Cure finishes to create a visually stunning box that increased sales by 20%.
Case Study 2: Cosmetic Product Launch
A beauty company utilized matte and textured Cast & Cure effects to differentiate its new skincare line, resulting in enhanced brand perception.
10. The Future of Cast & Cure in Paper Packaging
As sustainability becomes a top priority for brands and consumers alike, the demand for eco-friendly finishing techniques like Cast & Cure is expected to grow. Advances in casting film technology and UV curing systems will further expand the possibilities of this innovative process, ensuring its continued relevance in the packaging industry.
In conclusion, Cast & Cure is more than just a finishing technique—it’s a transformative solution for brands looking to create sustainable, cost-effective, and visually stunning packaging. Whether you’re in luxury goods, food and beverage, or cosmetics, Cast & Cure offers endless possibilities to elevate your packaging and captivate your audience.
Interested in exploring the application of these custom design & surface treatment processes in printing & packaging products? Click here to access our online showcases & guides…
Here at UGI, we design and manufacture various boxes for many industries:
Advertising boxes; bakery boxes; bottle boxes; candies boxes; cardboard boxes; drawer boxes; cigarettes boxes; file storages boxes; heart shaped boxes; medicine packaging; moving boxes; packaging gift boxes; paperboard packaging; product boxes; protective packaging; retail boxes; shipping cartons; napkin boxes; chipboard boxes; fruit vegetable boxes; electronic packaging boxes; card boxes; craft boxes; lunch boxes; display boxes; folding boxes; clear boxes; mailing boxes; chocolate boxes; cloth boxes; cake boxes; candle boxes; and as well as many others…
WORKING PROCESS
In order to get a smooth process to fulfill your order we suggest you follow below working process with UGI Packaging:
- Request a quote based on the specifications you require via email. Include any photos, images, art design, or technical sketch that could be helpful.
- If you have a similar or identical box to that which you require, send it (via UPS, TNT, DHL, or FEDEX) only after you are satisfied with our quote has been received.
- UGI Packaging will then provide you with a sample and a final quote with our technical sketch in PDF, AI, or CDR format. We will charge you for the sample or prototype development, but it should only be a nominal amounts. After receive your formal order, we will refund the sample charge as our negotiation.
- If you approve the sample then place your order and sign the contract, with 40% advance payment from you, we will start production.
- If any significant changes need to be made to the sample we strongly recommend checking 2nd samples from us before you confirm the final version.
Connect with us on WhatsApp to discuss your next packaging design solution with our manufacturing!